How Iron and Steel Recycling Works
Generation and collection of iron and steel scrap
Currently, approximately 25.5 million tons of city scrap (in FY2023) is collected and recycled each year, and the amount generated is closely related to the amount of cumulative steel stock. The term “cumulative steel stock” refers to the total amount of steel used in Japan that is still in the country in some form. This includes everything from buildings and bridges to automobiles, appliances, and razor blades. The current cumulative steel stock is over 1.41 billion tons (FY2021), and it continues to grow. The amount of iron and steel scrap generated has remained at around 2-3% of the cumulative steel stock, and the amount of iron and steel scrap generated is expected to increase in line with the increase in the cumulative steel stock.
There are various ways of collecting this scrap, but it is common for specialized collectors to collect it, or for scrap processors to process it after the non-ferrous materials and parts have been removed to some extent by demolition companies that dismantle buildings and vehicles.
Introduction to Each Processing Step
Guillotine shear:Processing process
Precise cutting of large structures, stable supply with high processing capacity
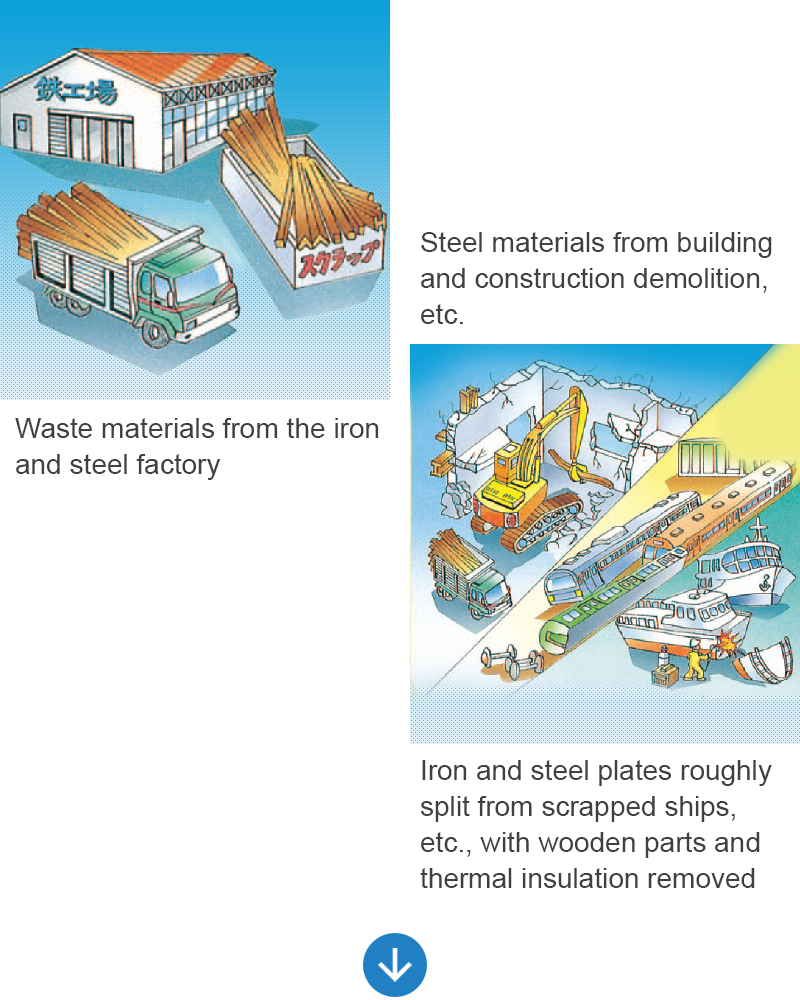
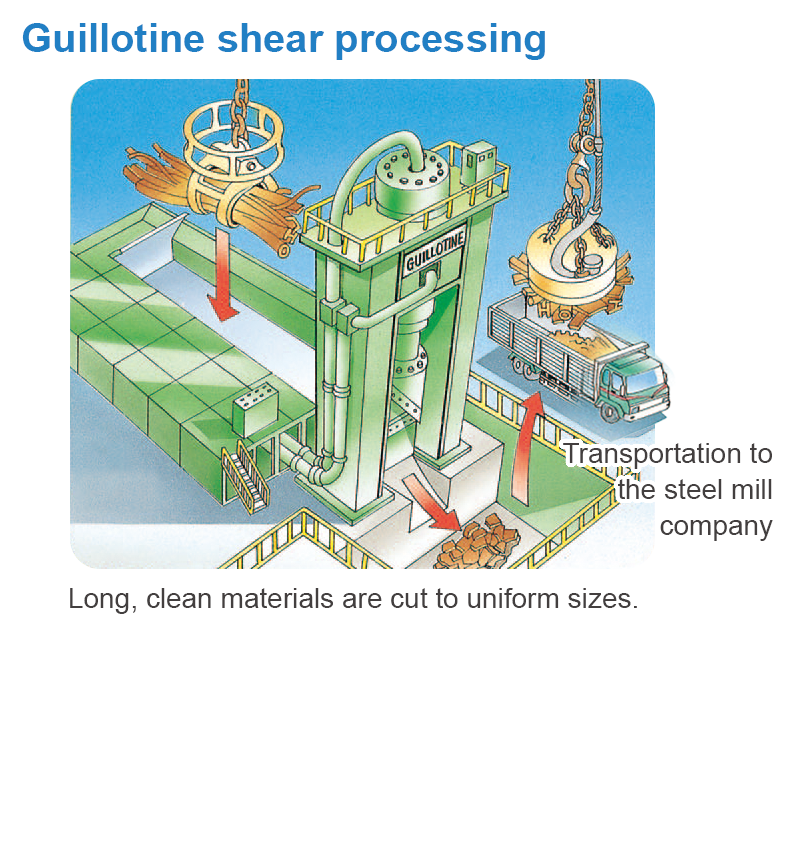
Shredder:Processing process
Provision of high-purity, high-specific gravity shredded products
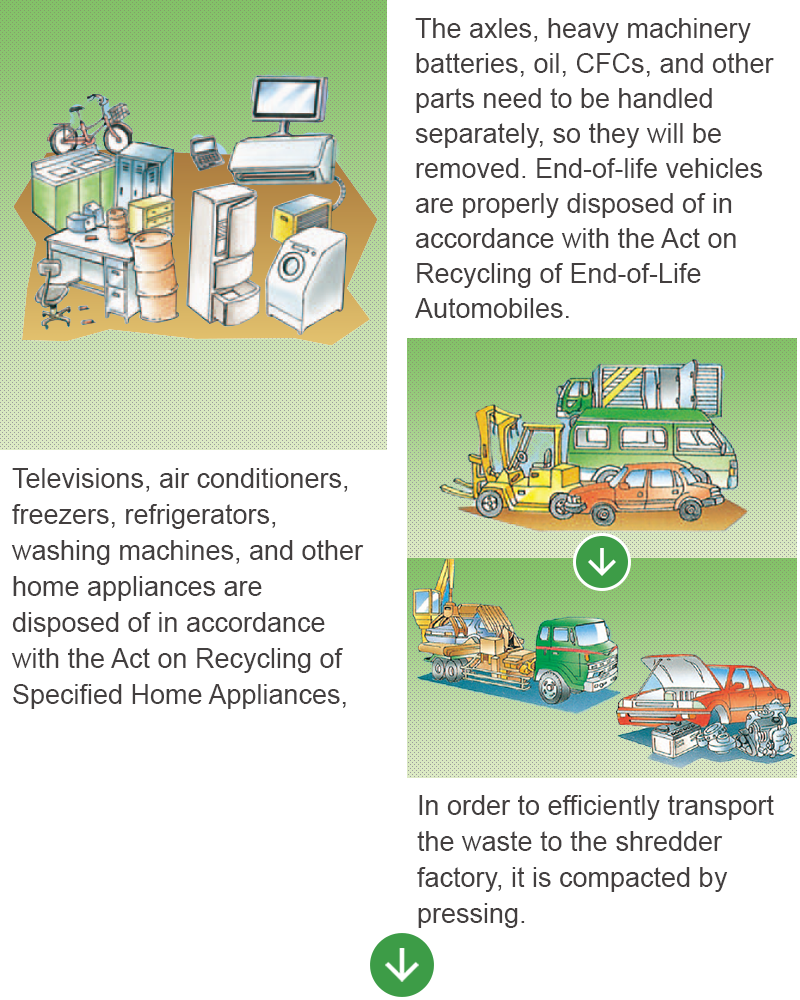
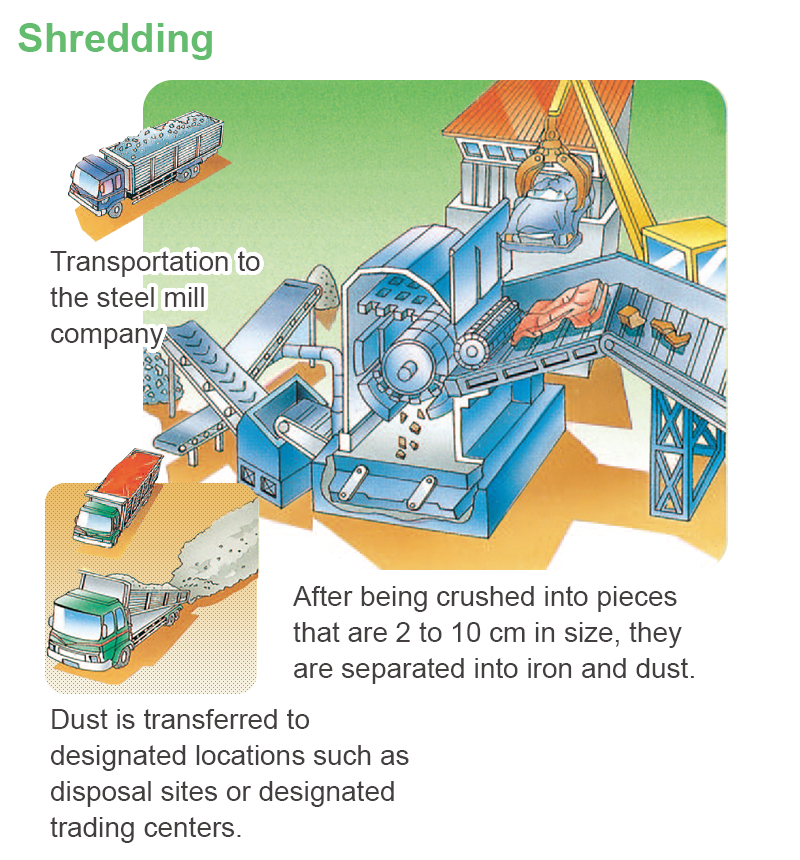
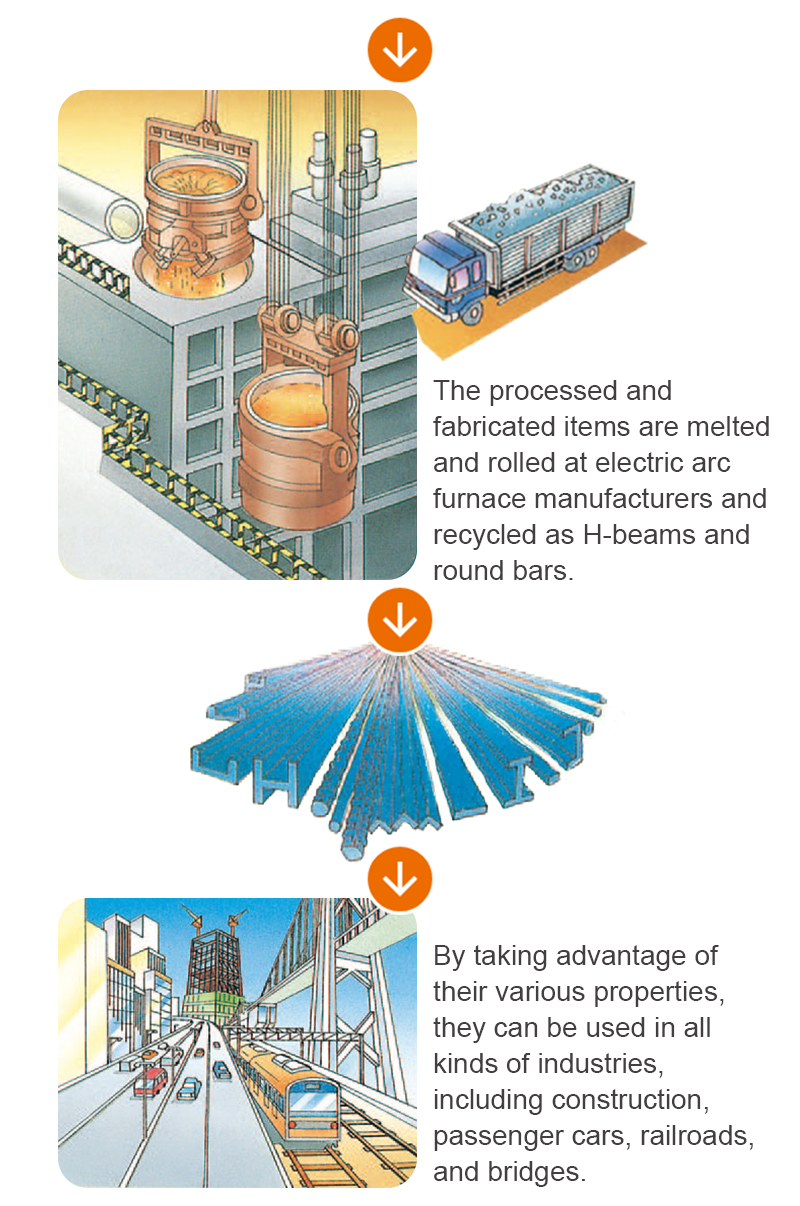
Steelmaking Processes Using Electric Arc Furnaces and Blast Furnaces
In the case of electric furnace steelmaking, the raw material used is iron and steel scrap. There are two types of induction heating: arc induction and high-frequency induction. Here we will explain the more common arc induction. This is a refining process in which an arc is passed between an electrode and the iron and steel scrap and the heat from the arc is used for refining. An electric arc furnace has a pot-like shape with a lid, and a thick graphite electrode is inserted vertically into the lid. When an electric current is applied, an arc is generated between the iron and steel scrap and the electrode, and the arc heat melts the iron and steel scrap. In this case, oxygen is blown in at high temperatures to obtain reaction heat. This process is called oxidizing refining, and it is followed by reducing refining, which removes oxygen and sulfur. In reduction refining, the oxidized slag (steelmaking dross) produced in oxidized refining is removed to the outside of the furnace, and then powdered coke, lime, etc., are added to form reduced slag. The powdered coke and lime are heated to a high temperature to form calcium carbide, which removes the carbon dioxide and sulfur dioxide. The steel is then further refined by adding powdered coke, ferrosilicon, etc., to bring it to the desired composition. The two-stage refining process of oxidizing and reducing is a feature of electric arc furnace steelmaking.
In the case of steelmaking using a blast furnace, there are two stages: ironmaking (pig iron making), in which pig iron is produced in a blast furnace (smelting furnace); and steelmaking, in which the pig iron is refined in a converter to produce various types of steel. The main body of the blast furnace is long and narrow, with a smaller part at the top like a sake bottle. Iron ore and coke are alternately charged and hot air at a temperature of about 1,200°C is blown into it. The coke then burns, raising the temperature of the furnace, and the iron is extracted from the iron ore and melts, collecting at the bottom of the furnace. This is called pig iron. The molten iron that flows out of the several tapholes is loaded into freight cars while still mostly molten, and after going through a process called “molten iron pretreatment” to remove silicon, phosphorus, and sulfur, it is transported to the steelmaking facility and charged into the converter (a squat, pot-shaped vessel). Pig iron contains a large amount of carbon (4-5%), which makes it hard and brittle. In order to make it into tenacious and tough steel, it is necessary to thoroughly reduce the carbon content and remove impurities that could not be removed by the preliminary treatment of the molten iron. This is the purpose of steelmaking. A small amount of iron and steel scrap is charged into the converter, and then molten pig iron is poured from a ladle into the tilted mouth of the converter. The furnace is set up again and the refining process begins. After adding quicklime and blowing in oxygen to remove impurities, the molten steel is solidified into a semi-finished product called a billet (a large mass of steel) using a continuous casting equipment, and given a rough shape called a slab, bloom, or billet. It is then heated and rolled by the rolling mill into various shapes such as wire rod, plate, sheet and steel pipe.
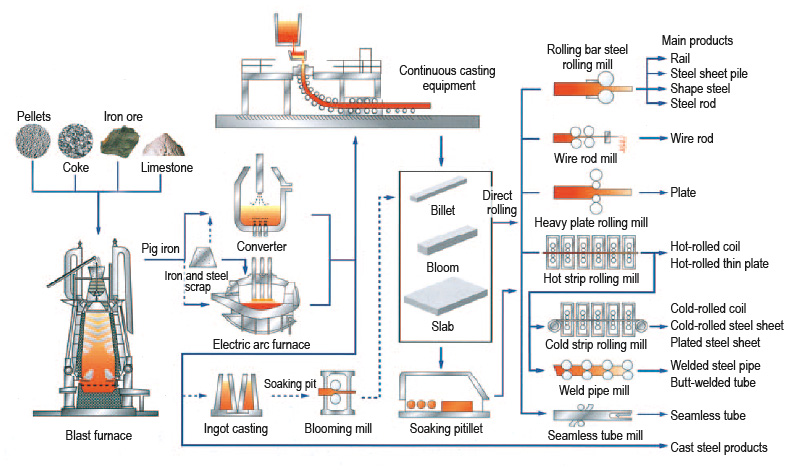